Poor Response / Lacking Power
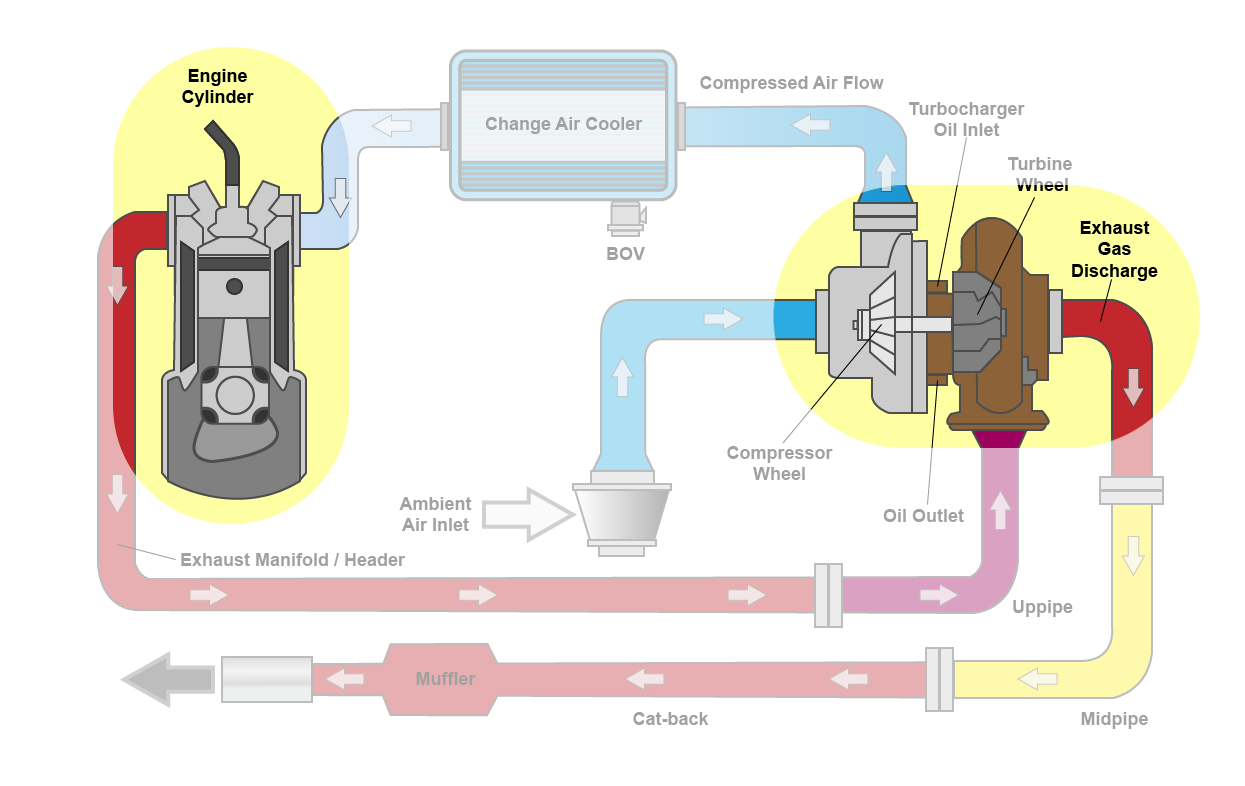
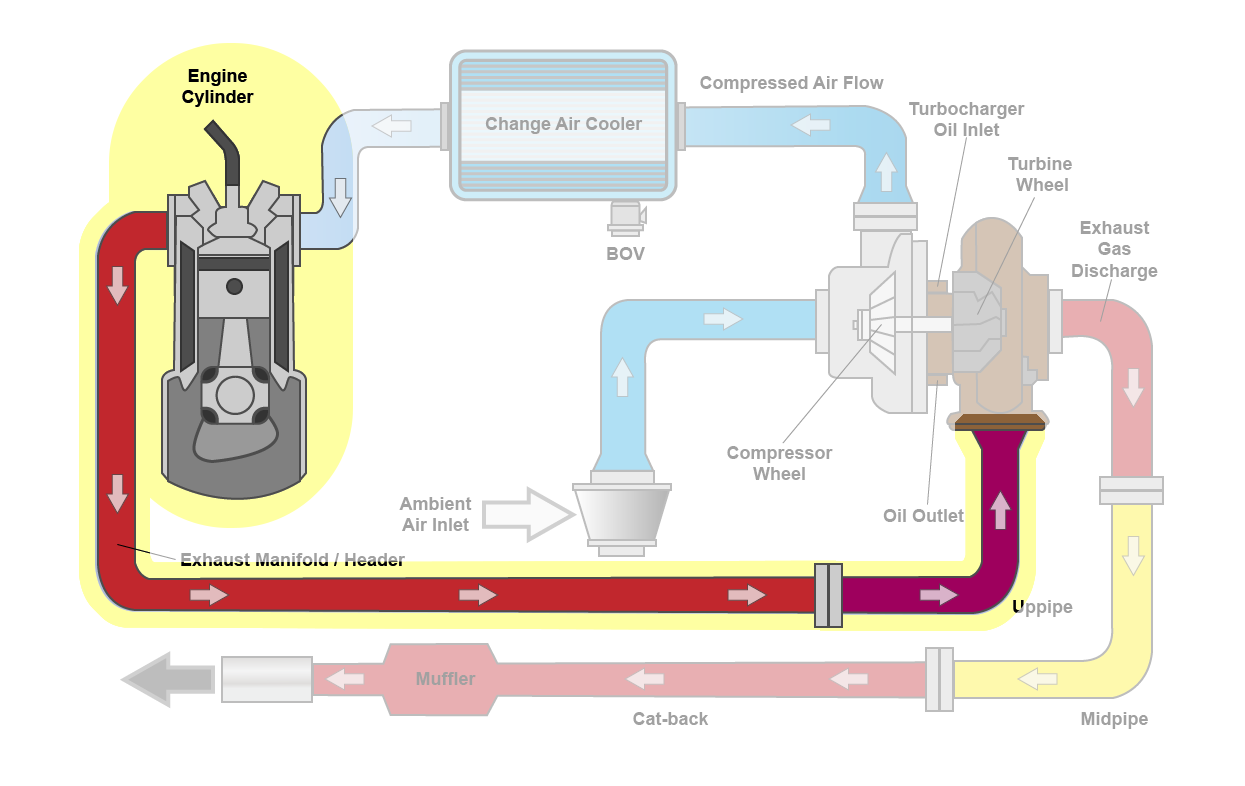
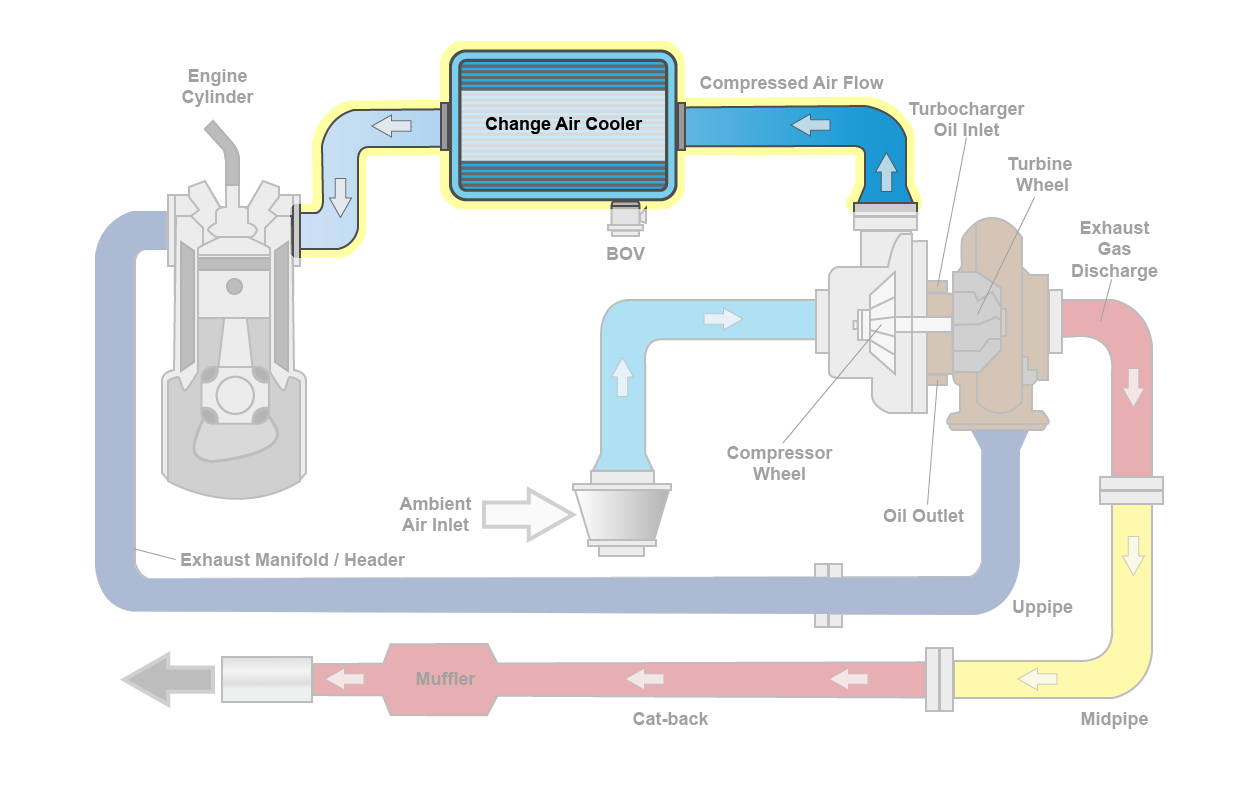
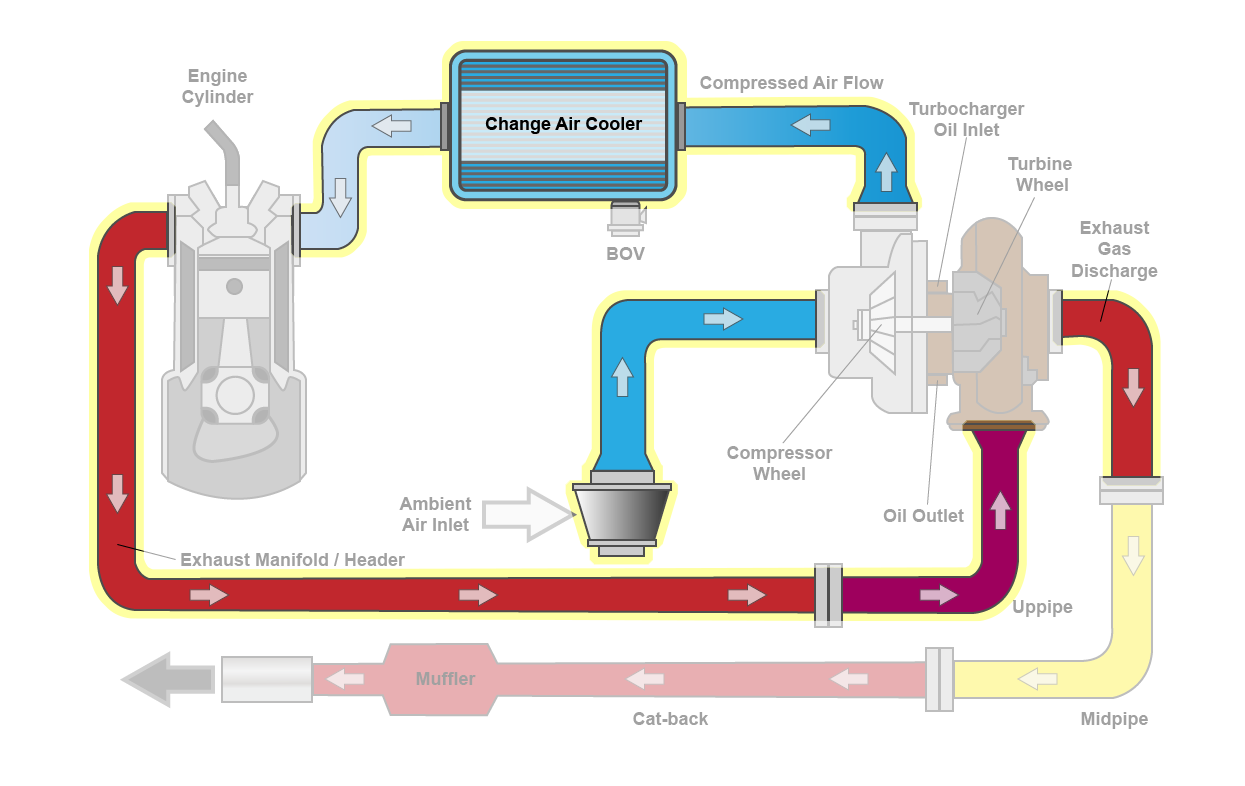
Turbo vacuum lines
Exhaust leak at turbo to engine manifold
Air leak in ducting or charge air cooler
Air or exhaust restriction
Engine failure
Turbo failure
Ignition failures
Fuel system failure
1) Carefully inspect all metal and rubber ductwork connections, seals, clamps, o-rings, gaskets associated with the turbocharger. Repair and replace as needed.
1) Inspect ducting for bending, collapsing, rust or deterioration. Remove ducting and inspect internally for oil or material restriction. Repair and replace as needed. Install new air filter per manufacturer recommendation.
2) Clogged charge air coolers can be reviewed with thermal evaluation guns across the cooler face. Temperature should drop from compressed air flow ducting across the charger cooler into the exiting ducting. Pressure should remain the same at the entry and exit of the cooler.
3) Muffler, converter or DPF filter can clog and restrict air flow. Any changes to air and ducting size can effect pressure and volume required to achieve correct turbo performance.